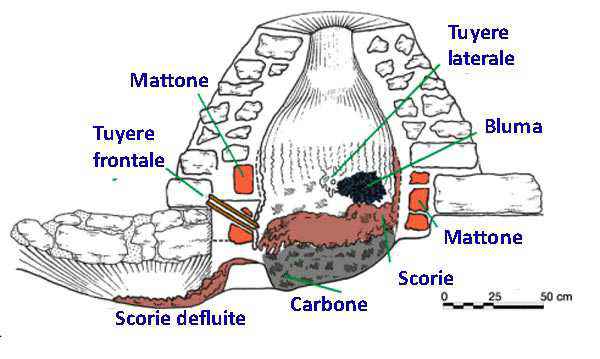
IL PRIMO FERRO
Tutti sanno che il primo ferro in Italia fu prodotto dagli Etruschi a partire da 8-10 secoli prima di Cristo. Ma forse non tutti conoscono come si arrivò a questo, che cosa ci fu dietro a questa importantissima scoperta e soprattutto che cosa questo fatto significò per i popoli Italici che vissero nell’arco del primo millennio avanti Cristo.
Proveremo a dare qualche risposta a questi quesiti prendendo per scenario le nostre zone dove certamente vide le luce il primo ferro italiano: il golfo di Follonica, tra i promontori di Piombino e Punta Ala, nelle città etrusche di Populonia e Vetulonia e nei territori da loro direttamente controllati.
Prima di parlare di antiche tecniche metallurgiche, credo che sia utile descrivere brevemente quale era le situazione nel bacino del Mediterraneo e davanti alle coste Italiane intorno al 1° Millennio a.C.
In quell’epoca era grande la fame di metalli quali il rame e lo stagno (che servivano a produrre il bronzo), metalli come l’oro e l’argento, per i gioielli delle classi più agiate, ma soprattutto navi provenienti da paesi orientali micenei, fenici ecc. ricercavano il metallo allora più prezioso: IL FERRO. Di gran lunga più duro di tutti gli altri e quindi adatto a fabbricare le armi ed a costruire gli attrezzi da lavoro per l’agricoltura.
Bisogna premettere che la metallurgia era una scienza conosciuta e praticata in Medio Oriente già molti secoli prima del periodo che stiamo esaminando.
In particolare gli Ittiti erano considerati dai Greci i creatori della Siderurgia (così come Apollonio da Rodio ci ha tramandato attraverso il poema epico le Argonautiche), un popolo che abitava nell’odierna Georgia, ad Est della Turchia, vicino il confine sovietico: era la leggendaria Colchide, verso la quale si diresse Giasone con i suoi Argonauti alla ricerca del vello d’oro.
Chiaramente questi popoli orientali, alla ricerca dei metalli, arrivarono ad esplorare anche le coste della nostra penisola e naturalmente quelle della Toscana, scoprendo gli immensi giacimenti dell’isola d’Elba, quelli delle colline metallifere e, più a Sud, quelli dei monti della Tolfa.
In ogni caso questi popoli, più progrediti di quelli con i quali vennero a contatto e portatori di nuove tecniche metallurgiche, aprirono quella che potremmo chiamare la via dei metalli. A questo punto (e siamo nel 9°-8° sec. a.C.) i popoli nativi delle zone più ricche di giacimenti metalliferi, non vollero restare fuori da questo enorme affare quali semplici spettatori, ma si organizzarono.
Così gli Etruschi, che sino ad allora erano vissuti in villaggi, compresero che i loro giacimenti di metalli non erano sufficientemente salvaguardati, né che si poteva organizzare e soddisfare questa enorme domanda esterna con una struttura quale quella dei complessi di abitati allora esistenti. Fu così che nell’8°-7° sec. i villaggi si fusero poco alla volta in centri più consistenti dando vita ad entità più vaste, creando una diversa urbanizzazione con specifiche zone di produzione, assicurando in questo modo a tali attività una direttiva, proveniente da un unico centro dotato di poteri decisionali e più adatto alle esigenze del nuovo mercato. Nacquero cosi alcune delle Città-stato etrusche e nello stesso tempo nasceva L’età del ferro.
Dunque furono gli stessi Etruschi a sfruttare la ricchezza metallurgica che si trovava nei loro territori e seppero gestire in maniera straordinaria questa loro opportunità: allora come oggi, i minerali o le materie prime, siano esse il petrolio, il silicio per l’elettronica, l’uranio per l’energia nucleare o altri minerali preziosi, hanno reso ricchi i popoli.
Il ferro lavorato, allo stato di minerale o sotto forma di spugne, rappresentò il più diffuso oggetto di scambio per gli Etruschi che adottarono ed affinarono le tecniche metallurgiche degli orientali: questo scambio si rivelò immensamente proficuo per questo popolo il quale, insieme ad oggetti preziosi, assorbì la civiltà dell’Oriente antico e la trasferì sul suolo dell’Occidente europeo. Si ritrovano così nelle tombe etrusche dell’8-6° sec. a.C. veri e propri tesori in oro, vasellame dipinto, oggetti di artigianato, vetro, tessuti, ma nello stesso tempo furono acquisiti in quel periodo l’alfabeto, alcune divinità ed anche le coltivazioni della vite e dell’olivo.
Sembra oramai certo che gli Etruschi, oltre agli oggetti ed alla tecnica, fecero venire anche alcuni artigiani per le lavorazioni dei metalli e delle ceramiche, i quali insegnarono loro a copiare gli oggetti e ad adattarli al proprio gusto: questo fu il risultato della lavorazione e della esportazione dei metalli e del ferro in particolare, ferro che era considerato prezioso, quasi fosse un dono divino, cosi come Servio, nel 4° sec. a.C. commentava a proposito dell’Elba:
“…. mentre nelle altre regioni lo sfruttamento dell’attività estrattiva isterilisce i filoni del materiale, all’Isola d’Elba il metallo asportato, straordinariamente si rigenera e così può di nuovo essere estratto dagli stessi luoghi…”
Furono proprio le miniere dell’Elba le più importanti dell’antichità. L’isola era controllata dalla città di Populonia: unico grande centro etrusco situato direttamente sul mare. Questa posizione particolare le fu estremamente favorevole, avvantaggiandola nei contatti commerciali e negli scambi culturali.
L’Elba era ricchissima di metalli e si calcola che, a partire dal 750-700 a.C., venissero estratte circa 10.000 tons di minerale all’anno per un periodo di circa 400 anni.
All’inizio il minerale veniva lavorato in loco, ma successivamente la fusione fu trasferita direttamente sulla terraferma alle pendici della collina di Populonia. Le prime tracce della lavorazione del ferro nel bellissimo golfo di Baratti, risalgono al 5°-6° sec. e si presume che questo trasferimento sia avvenuto forse a causa dell’esaurirsi del “legno duro”, quello di quercia e di leccio necessario per la fusione, ma il fatto che sicuramente favorì lo spostamento di queste attività fu la battaglia di Cuma (474 a.C.) con la conseguente perdita da parte degli Etruschi della loro supremazia sul mare Tirreno che passò ai Greci e quindi mise in serio pericolo la produzione nell’isola.
Con questo stato di cose, l’attività era ritenuta più sicura a Baratti e successivamente lungo tutta la costa tra S. Vincenzo e Punta Ala. Fatto è che la lavorazione del ferro a Baratti fu così intensa (è stato stimato che siano state estratte circa 500.000 tons di ferro), che le scorie di lavorazione, le così dette loppe ricoprirono un po’ alla volta e per molti metri, intere necropoli dei secoli precedenti. Queste tombe, alcune delle quali grandiose come quelle dei Carri con un tumulo di 28 metri di diametro, furono riscoperte solo quando, negli anni compresi tra il 1915 ed il 1959, alcune società industriali recuperarono le scorie antiche per ricavarne ancora ferro. Queste loppe infatti contenevano ancora circa il 75% del ferro totale del precedente minerale, cioè avevano ancora un tenore di ferro del 50%, mentre gli Etruschi riuscivano ad estrarne solo il 15% circa. Per dare un’idea della differenza, basti pensare che, con i moderni impianti, si riesce a sfruttare il minerale oltre il 96% del suo contenuto in ferro.
Una notizia storicamente certa è quella secondo la quale nel 205 a.C. (già sotto il dominio di Roma) Populonia fornisce un quantitativo di ferro per la spedizione in Africa di Publio Cornelio Scipione contro Annibale.
Altra importantissima zona per quanto riguarda la produzione di ferro, controllata dalla stessa Populonia, era quella del Campigliese, distante 10-12 Km. dal mare. Qui sono stati rintracciati numerosi resti di antiche fornaci che risalgono all’ 8° sec.; in questi luoghi infatti venivano sin dal periodo Villanoviano sfruttati giacimenti di Solfuri di Rame, piombo e zinco oltre a calcopirite e galena argentifere, di rame e, in misura minore ma non meno importanti, quelli di stagno.
Altro polo industriale era la città etrusca di Vetulonia della quale si conserva ancora una parte delle mura inglobate nell’odierno abitato. Questa era, all’inizio dell’età del ferro, già famosa per i minerali che i minatori estraevano dalle miniere delle colline metallifere circostanti, quali il ferro, il rame, l’argento, il piombo, mentre la presenza in quell’epoca del grande lago marino chiamato Prilie ai piedi della collina sulla quale sorgeva Vetulonia, permise ben presto l’apertura di vie commerciali lungo le quali far partire i prodotti delle metallurgia e far arrivare nella città altri materiali pregiati.
Questa opportunità le permise fino alla metà del 6° sec. a.C., di dominare tutti i territori circostanti fino a Piombino e quindi anche la stessa Populonia. I vetuloniesi scambiavano il loro rame con l’oro punico e greco e divennero famosissimi orafi, come dimostrano gli straordinari gioielli decorati con tecniche dette “a pulviscolo”, “a granulazione”, “a sbalzo”, “a filigrana” di numerose tombe dell’ 8°- 7° sec. tra le quali spicca, per i tesori ritrovati, quella detta “Del Littore”.
Vetulonia era quindi il centro dirigenziale di un grande territorio composto da numerosi abitati sorti in funzione della estrazione e/o lavorazione dei metalli. Il più famoso è sicuramente l’abitato del Lago dell’Accesa nel comune di Massa Marittima, che recenti scavi hanno riportato alla luce.
Questo villaggio, posto vicino alla sorgente del fiume Bruna, lo stesso che scorre sotto Vetulonia, era sicuramente legato alle vicine miniere di pirite e calcopirite, destinato ad ospitare non tanto i minatori che vivevano presumibilmente in capanne, quanto i “Maestri” e i “Dirigenti” dell’impresa, come stanno a dimostrare la complessità delle abitazioni che avevano già tetti formati da tegole di copertura.
Per cause ancora non chiare, nel corso del 6° sec. il grande centro dell’industria metallotecnica di Vetulonia accusò una improvvisa decadenza ed il predominio passò a Populonia che lo terrà fino a tutto il 3° sec. a.C. lavorando di continuo il ferro elbano.
LE TECNICHE DI LAVORAZIONE
Già Plinio Il Vecchio parla della escavazione delle miniere nel mondo antico e, parlando delle condizioni di lavoro dei minatori, dice testualmente: “…cavano le montagne seguendo cunicoli aperti per lungo tratto a lume di lucerne. Per molti mesi non vedono giorno…”. Anche Cassiodoro ne parla aggiungendo alcuni particolari: “…si entra sotto terra con abilità e si cerca i tesori della ricca natura. Gli uomini entrano nella profonda oscurità e vivono lontano della luce del sole: può succedere che per qualche crollo non possono più tornare indietro, tuttavia quelli che usano molta cautela sono i più fortunati ed entrano poveri ma escono ricchi. Quando poi sono ritornati alla luce separano dalla terra le parti più piccole e quelle più pesanti e procedono alla cottura in un grande forno costruito con materiale fittile fino al momento della fusione”. Aggiunge Diodoro Siculo, a proposito dell’isola d’Elba: “…. vicino alla città chiamata Populonia v’è un’isola chiamata AITHALIA che dista dalla riva circa 100 stadi, prese il nome dalla quantità di fuliggine presente su di essa. Infatti contiene minerale di ferro in gran quantità che viene ridotto in pezzi per essere fuso. I lavoratori spezzano la pietra e bruciano i vari pezzi in fornaci costruite a regole d’arte fondendoli in queste con una gran quantità di fuoco e ne fanno pezzi simili a grandi spugne. Alcuni trafficanti li comprano e li smistano negli empori…”
E’ comunque evidente che, nella storia della metallurgia, il trattamento del minerale di ferro avvenne dopo quello di altri minerali e questo si spiega con le più alte temperature necessarie per la estrazione del metallo vero e proprio: con il tempo ci fu quindi un continuo perfezionamento della siderurgia. Ci sembra interessante descrivere, almeno alla luce delle più recenti scoperte e delle teorie più qualificate, quale fosse il funzionamento dei forni per la cottura del minerale di ferro; forni che venivano usati solo una volta dal momento che dovevano essere distrutti, dopo il raffreddamento della massa incandescente, per il recupero dei metalli depositatisi sul fondo.
Questi manufatti erano formati da un crogiuolo incassato nel terreno, rivestito in pietra arenaria locale dove si raccoglieva il metallo e da un cumulo verticale, cilindrico o tronco-conico, che fungeva da mantello di contenimento.
Il forno aveva un diametro interno di circa 40 cm., un’altezza di circa mt. 1,5. ed era formato anch’esso da pietra arenaria che, con il calore, compattava i blocchi tra loro; tra questi erano inserite numerose stuccature in argilla in modo da rendere il tutto perfettamente cementato.
Sono proprio questi pezzi di argilla, che è ancora facile ritrovare tra i boschi e lungo tutto il litorale del Golfo di Follonica, che segnalano la presenza di un antico forno fusorio. Questi ammassi mostrano chiaramente la parte che era rivolta verso l’interno del forno con numerose colature di metallo, mentre hanno l’altra faccia di un colore rossastro dovuto alla cottura dell’argilla stessa.
Il minerale era posto in questa camera in strati alternati con carbone di legna di pino o quercia, dopo averlo spezzettato in piccole parti sia per depurarlo del materiale inerte, sia per facilitarne la cottura. Particolare accuratezza veniva posta nella scelta del luogo di lavorazione, dato che il tiraggio doveva essere assicurato da una naturale corrente d’aria ascendente.
E’ probabile che gli Etruschi adottassero anche un sistema di insufflaggio forzato di aria probabilmente con mantici in pelle, attraverso fori fatti in zone particolari del cumulo, proprio come i carbonai di oggi li praticano nelle pareti delle loro carbonaie.
Una volta acceso il forno, non era comunque possibile raggiungere le temperature necessarie alla completa fusione del ferro, come avveniva invece per il rame e per altri metalli con un punto di fusione più basso, ma il ferro si raccoglieva sul fondo del forno, nel crogiuolo, allo stato pastoso come una massa spugnosa mista a cenere e carbone.
Le scorie, più leggere e quindi stratificate sopra alla massa, venivano già in parte eliminate attraverso il loro deflusso da un’apertura praticata al livello poco superiore del crogiuolo stesso.
Per il recupero del massello prodotto, pesante circa 40-50 Kg., doveva necessariamente essere distrutto il forno ed è per questo motivo che sono così scarse le tracce di tali strutture.
Il ferro grezzo così ottenuto, veniva poi liberato dalle ulteriori scorie e dalle impurità attraverso una successiva lavorazione di fucinatura consistente in fasi alternate di riscaldamento ad elevate temperature e di martellamenti successivi.
Ma vediamo più da vicino come era fatto il ferro ottenuto con le tecniche prima descritte. Per capire meglio quale sia la differenza che intercorre tra il ferro prodotto 2500 anni fa ed un normale acciaio di oggi, abbiamo rappresentato fotograficamente, attraverso un microscopio metallografico, la microstruttura di un pezzo di ferro trovato a Populonia durante il recupero delle scorie avvenuto negli anni ’50 e la sezione di un attuale chiodo da carpenteria.
Dal punto di vista chimico-fisico, si può parlare di Ferro Puro con struttura solo ferritica nel primo caso, mentre nel secondo caso si nota una soluzione solida di Carbonio nel ferro che ha conferito alla lega una maggiore durezza del metallo precedente e quindi si può parlare di ACCIAIO.
Oggi e Piombino, a pochissima distanza dalla zona industriale etrusca di Populonia, funziona a pieno ritmo un moderno centro siderurgico che produce con i suoi altiforni migliaia di tonnellate di acciaio.
Altri impianti si trovano nei dintorni di questa città, ma chi viene da queste parti non può fare a meno di pensare a questi antichi fabbri i quali, rubato una notte il segreto al Dio Vulcano, così come raccontano numerosi miti, si tramandarono i segreti iniziatici del mestiere di fondere il metallo.
Da quando si cominciò ad estrarre minerali dalle Colline Metallifere sono passate alcune migliaia di anni. Oggi, nel terzo millennio e grazie a quel minerale estratto, l’uomo si muove a velocità incredibili, è andato sulla luna, indaga l’infinitamente grande e l’infinitamente piccolo. Qui è nata e si è sviluppata la siderurgia italiana. Come abbiamo visto, questo è stato possibile grazie alla grande disponibilità di materia prima come i minerali, il combustibile per la loro fusione, l’acqua per muovere i mantici, l’argilla per la costruzione dei primi forni, ma soprattutto grazie all’arte, alle fatiche ed al sacrificio di chi ha dato tutto, spesso anche la vita stessa, per andare sotto terra
TAVOLA DEL FR.’. M. L.